Increasingly complex ECUs and crowded circuit boards demand more thorough evaluation for reliability and long-term performance
Twenty years ago, automotive testing focused mainly on mechanical systems – engine performance, suspension, brakes, etc. However, as electronic features in cars have become the norm across the industry, testing has had to evolve. Modern testing now goes far beyond mechanical systems to assess the durability and long-term performance of the electronic control units, sensors and embedded software that are so critical to the performance of today’s vehicles.
Modern vehicles have anywhere from 80 to more than 150 ECUs that individually manage features such as the air-conditioning, braking systems, keyless entry, crash detection and mitigation. These ECUs may be located on separate circuit boards that need to be tested individually for functionality, reliability and performance.
A critical aspect of overall ECU testing is evaluating the strength of the circuit board. The durability of the board is vital, and it must undergo extensive real-world simulation testing to ensure it can withstand bumpy roads and sudden impacts without failure. The electrical signal flowing through the board needs to be monitored while these tests are performed, to provide feedback about how the board will react in high-stress environments. As ECUs have increased in complexity, the circuit board has become more crowded. Each soldered connection requires a weld test to provide a comprehensive evaluation of the quality of the board.
With many of these ECUs contributing to modern safety features, it is essential that they be tested with the utmost care.
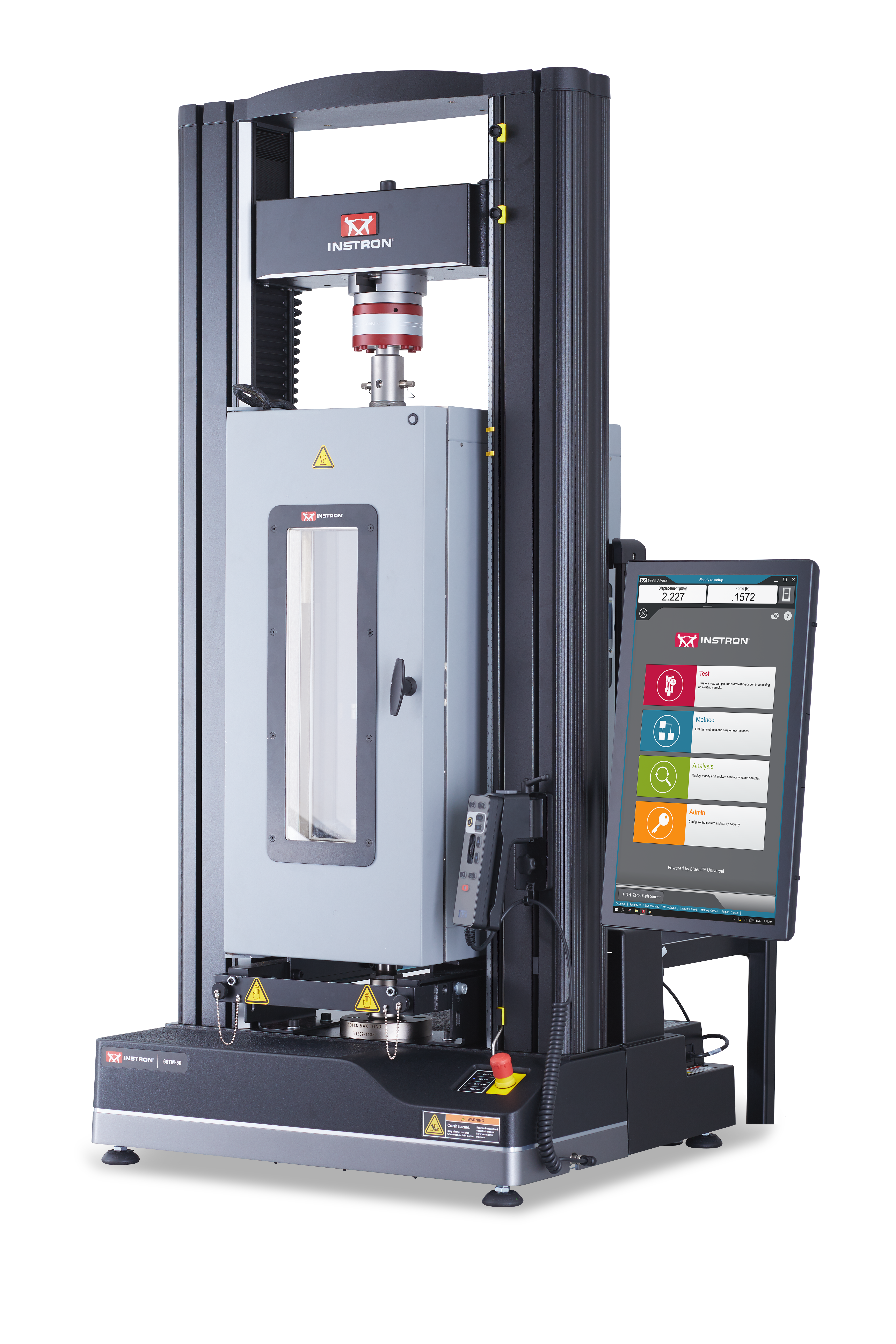
Another major change in modern automotive design is the presence of at least one touchscreen in virtually every new vehicle. This introduces new test requirements for the accuracy and responsiveness of the screen. Without haptic feedback, the user requires a high level of confidence in the sensitivity and precision of the screen. Automated probes can be used to mimic how the user interacts with the screen: by sending the probe to a specified location while simultaneously recording the electric response of the screen, the latency and accuracy of the system can be measured. This provides an understanding of how the system will perform in real-world situations.
The screens in vehicles are increasing in number and size. As the screens get bigger, their geometry changes, curving to fit the confines of the dashboard. This new geometry requires more flexible materials and different adhesives and assembly methods – all of which demand more testing.
Finally, environmental temperature testing is a crucial aspect of performance evaluation for all vehicles with electrical components. The scope of this type of testing has increased with the evolution of electric vehicles. Electric and hybrid vehicles are equipped with battery management systems that regulate the charging process and ensure the batteries remain within safe operational bounds. The effectiveness of these battery management systems should be evaluated in high- and low-temperature environments. Extreme temperatures can reduce the lifespan of the battery or lead to thermal runaway. Tests can be designed using temperature chambers to replicate these conditions, enabling researchers and OEMs to understand how the system behaves under various environmental stresses.
Need to know
- ECU evaluation today is a very different animal from what it was in the past
- The durability of circuit boards in automotive electronics is vital, requiring rigorous testing
- Instron is a specialist developer of advanced reliability and stress test equipment