New measurement technology from WOM Testing Technologies now makes it possible to directly capture tire behavior in real-world conditions. ATTI sits down with Carlos Nerini, the company’s managing director and co-founder, to discuss how the solution came to life
For over 70 years, tire and chassis system modeling has depended largely on indoor testing. However, these controlled environments fall short in replicating real-world conditions, especially on snow and ice, where indoor testing faces serious limitations. As the demand for realistic vehicle dynamics simulations grows, accurately capturing tire behavior in real-world settings remains a major challenge – primarily due to the difficulty of measuring forces and moments directly at the contact patch.
The Wheel Orientation Measurement (WOM) device developed by WOM Testing Technologies, which was shortlisted for Testing Hardware Innovation of the Year at this year’s ATTI Awards, represents a breakthrough in this area. It adopts a unique approach to simulating longitudinal grip, using advanced measurement equipment to capture the dynamic loaded radius of a tire under real-world conditions. The embedded technology enables direct measurement of tire behavior in real-world conditions, overcoming multiple challenges that have hindered accurate on-vehicle tire characterization for decades, including:
- Acquisition of tire forces and moments at the contact patch and different reference systems, such as ISO-C, ISO-H and ISO-W.
- Secure sensor mounting on a moving wheel without compromising integrity.
- Conducting precise measurements on wet, snowy and icy roads.
What initially led you to question the use of a non-physical tire radius for longitudinal grip characterization?
The key issue is that the traditional reference radius (Re) leads to an inconsistent slip ratio (SR) when applied to real-world driving and braking scenarios. More specifically, the conventional reference radius is a physical measurement tied to an event different from what actually occurs in the tire during real driving conditions. That’s why I refer to it as non-physical – it does not physically manifest when the tire is actively generating grip on the road.
You mention that limited research has explored the impacts of this convention on tire modeling and real-time simulation. What simulation limitations arise from slip ratio convention, and why is research in this area limited?
Simulation is only as accurate as the models it relies on. Using a non-physical Re introduces errors in wheel angular velocity within the simulation loop – one of the key parameters for stability control and autonomous driving systems. Additionally, historical inconsistencies between grip characterization standards and slip ratio modeling introduce further errors in simulated grip.
Research in this area has been limited primarily due to a lack of technology for validating slip ratio under real-world conditions. Historically, tire testing was conducted almost exclusively indoors, shaping tire knowledge based on what could be observed in a controlled environment. These laboratory findings were never validated in real-world conditions simply because the necessary technology did not exist.
That’s why we developed the WOM device. Our technology is now reshaping our understanding of tires, and when combined with advanced AI-driven data engineering techniques, we can extract valuable insights from vast, complex datasets. This breakthrough has already improved longitudinal grip characterization – and there’s much more to uncover.
Your research uses cutting-edge technology to measure the dynamic loaded radius in real-world conditions. How did you develop this system and what does it consist of?
The system was developed as part of an applied research initiative in 2018, with the goal of deriving a tire force and moment (F&M) model based on real-world measurements. We realized that to achieve this, we needed to invent a device capable of instantaneously translating F&M data from the wheel force transducer measurement point to the tire contact patch. Without this transformation, obtaining a tire model from direct on-vehicle measurements would be impossible. While simulation-based models exist, they lack absolute certainty – WOM was created to bridge this gap.
The WOM device consists of multiple optical sensors rigidly attached to a subframe fixed to the wheel plane. This setup enables instantaneous measurement of wheel kinematics, the contact patch plane, dynamic loaded radius and the theoretical point of contact (P), enabling direct force and moment calculations at the contact patch.
Designed for ease of use, the WOM integrates seamlessly with existing sensing technologies, including temperature sensors, pressure sensors, slip velocity sensors, WFTs and cameras. In terms of datasets, it essentially provides laboratory-grade testing capabilities, directly on a moving vehicle.
What makes this technology groundbreaking compared to previous measurement methods?
Prior to WOM, no technology could directly measure real tire-road grip at the contact patch, including wheel angles relative to the ground, under any real-world condition. That is what makes this technology unique.
What were some of the biggest challenges in accurately capturing these real-world measurements?
Developing sensing technology capable of measuring on all surfaces, including ice, wet roads and other real-world conditions. Creating modular devices adaptable to any wheel on any vehicle integrable with multiple sensing technology. Establishing an engineering workflow that processes real-world data into usable, highly realistic virtual tire models while overcoming the limitations of on-road measurements – known as TiReC (Tire in Real Condition Engineering Solution).
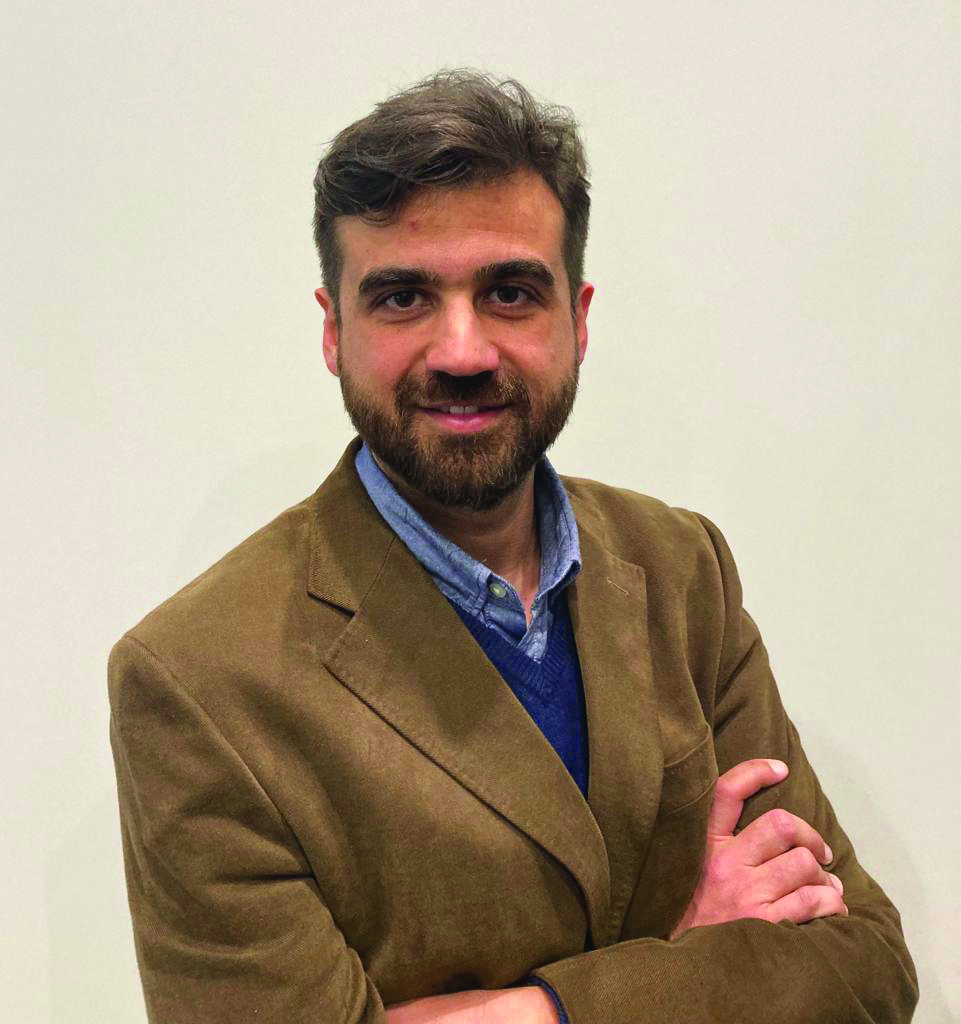
What studies have you conducted to prove out the effectiveness of the equipment and what were the results?
Since WOM is the first technology capable of capturing real-world tire data, there is no other ‘validation technology’. However, we conducted a back-to-back comparison of two tire models – one developed using TiReC and another based on traditional indoor testing.
We tested both models in a professional dynamic driver simulator, and two drivers independently confirmed that the TiReC-based model felt significantly closer to real-world performance.
Additionally, we applied the TiReC methodology to a wet track scenario, enabling our partners to develop an electronic stability control system entirely in a virtual environment – eliminating the need for physical prototypes, something previously impossible in traditional vehicle development without accurate wet models.
Regarding measurement consistency, we validated our data by comparing key parameters against other established technologies, showing strong correlation. We also implemented repeatability validation under both static and dynamic conditions, with outstanding results. The method relies on multiple optical triangulations, which intrinsically ensures precision and reliability through well-established sensing technology.
Have you encountered resistance from industry professionals regarding changing the slip ratio convention?
Tire Technology Expo 2025 was the first time we publicly presented our research on longitudinal grip characterization and modeling. Ultimately, whether or not the industry fully adopts our proposal, the most important outcome is fostering a discussion among researchers and engineers. With modern technology enabling new insights, this debate will help drive the next evolution in tire modeling.
What are the next steps for the work?
Our next priority is industrializing and scaling the application while exploring how it can enhance traditional testing methodologies.
More on tire modeling in the September edition of ATTI. Read the latest issue for FREE now